Advisor
Dr. Jennifer Jacobs - Media Arts & Technology, Computer Science
Mentor
Ashley Del Valle - Media Arts & Technology
Exploring the Expressive Opportunities of Cam-Based Design for Toolpath-level Control of 3D Printing
Interns
Ronan Hughes - Physics
Vitaliy Laptev - Chemical Engineering
Basant Seleym - Biopsychology
Kevin Nguyen - Computer Engineering
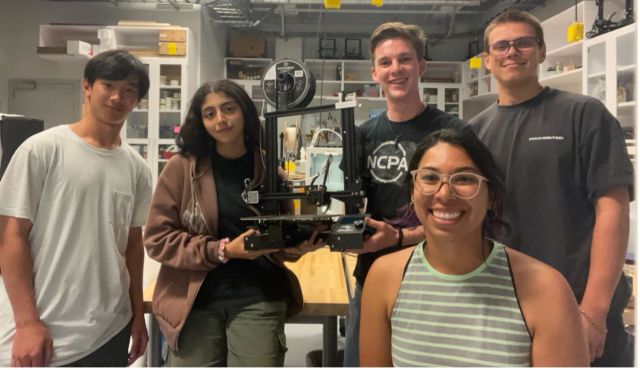
Project Description
The techniques, methods, and technologies used in 3D printing are constantly evolving, along with the demand for faster, more accurate, and higher-quality designs. One such technique, called Computer-Aided Manufacturing (CAM), is a design method to create machine instructions, known as G-Code, to control the machine parameters of 3D printers. G-code allows designers to interact with the components of a 3D printer directly, giving instructions to control parameters such as nozzle height, path, temperature, and material flow rate. This is used in manufacturing or producing 3D objects, for projects that may be personal for artistic designs or even in industry. Controlling these parameters will minimize computer error and the negative effects of material and environmental inconsistencies, such as filament and air temperature. Such control allows for the production of a variety of shapes and textures, including intricately designed and complex patterns. This facilitates accurate and timely prints. Despite CAM’s innovations, the techniques and processes remain poorly understood. Using p5.fab, a coding library used in designing 3D objects, we experimented with different shapes and lines by adjusting their G-code. Through this process, we discovered and documented the characteristics of different filament rates being extruded from a nozzle of gradually increasing height. This produced coil-like patterns that varied based on extrusion rate and height. Exploring these nontraditional toolpaths allowed us to create complex yet replicable designs. Overall, enhancing and documenting the workflow of CAM-based design enables future users to maximize the accuracy and complexity of their designs. Further optimization of this 3D modeling tool can expand implementations of CAM in fields such as medicine, aerospace, art, and various other industries.